When, Why & How to Replace a Cartridge Filter
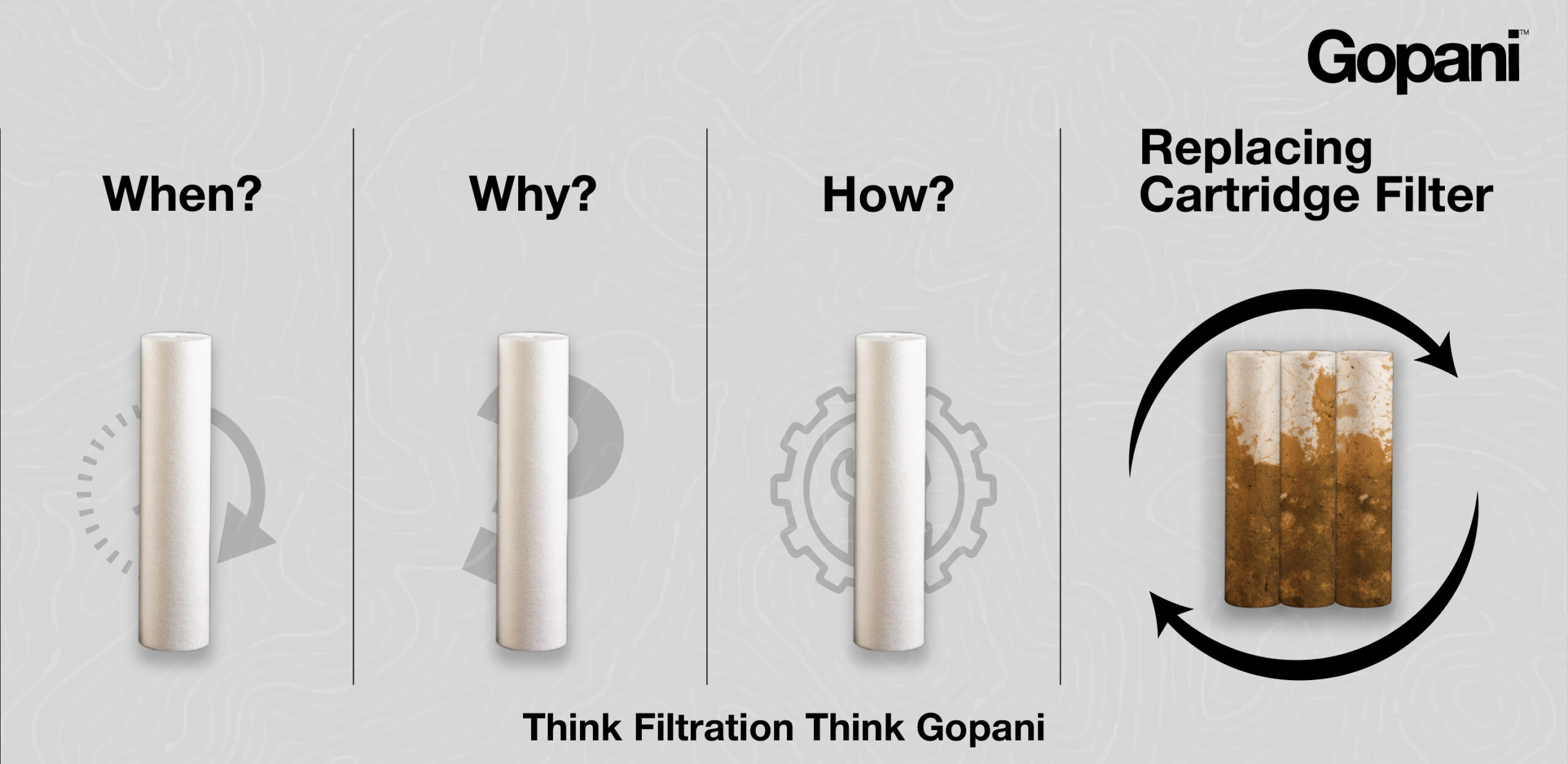
Filtration is a fundamental process in industries such as water treatment, pharmaceuticals, food and beverage, and petrochemicals etc. Cartridge filters, often the backbone of these systems, perform high-precision filtration, ensuring contaminants are removed effectively. Over time, as filters trap particulates, their performance declines, increasing system pressure and reducing flow rates. Replacing these filters on time is critical not only for maintaining operational efficiency but also for avoiding potential damage to equipment and contamination of products.
This guide provides an in-depth understanding of filter types, signs that indicate replacement is necessary, and a detailed procedural framework for cartridge replacement.
Types of Cartridge Filters
Cartridge filters are broadly classified into two types: depth filters and surface filters, each designed for distinct filtration applications.
Depth Filters
Depth filters are multi-layered media designed to trap particles throughout the thickness of the filter media. These filters excel in retaining a wide range of particle sizes, making them suitable for applications with high levels of particulates.
- Technical Construction:
Depth filters are typically made from fibrous materials such as cellulose, fiberglass, or polypropylene. These fibers are arranged in a gradient density format, where the outer layers capture larger particles while the finer inner layers trap smaller contaminants. - Advantages:
- High dirt-holding capacity due to volumetric filtration.
- Longer operational lifespan in high-particulate environments.
- Cost-effective for pre-filtration and high-load applications.
- Limitations:
- Less effective for precise particle size removal compared to surface filters.
- Filtration efficiency changes with clogging flow rate drops.
Surface Filters
Surface filters capture particles on their outer surface, providing precise and consistent filtration. These filters are often pleated to increase the filtration surface area while maintaining a compact size.
- Technical Construction:
Surface filters are made from membranes like polyester, nylon, Polypropylene, PES, PVDF, PTFE, or stainless steel mesh, with uniform pore sizes for selective filtration. - Advantages:
- High filtration precision due to consistent pore size.
- Suitable for final filtration stages requiring sterile or ultra-pure outputs.
- Easy to clean and reuse in some designs (e.g., stainless steel filters).
- Limitations:
- Lower dirt-holding capacity compared to depth filters.
- Susceptible to clogging in high-load applications without pre-filtration.
Difference Between Depth and Surface Filters
Depth Filters
- Multilayer structure
- Traps particles throughout media
- High dirt-holding capacity
- Suitable for high particulate loads
Surface Filters
- Single-layer structure
- Double Layer
- Captures particles on surface
- High filtration precision
- Suitable for fine particle contaminant filtration
When to Replace a Cartridge Filter
Pressure Differential Monitoring
The most reliable metric for determining when to replace a cartridge filter is the pressure differential (ΔP) across the filter. As particulates accumulate, ΔP rises. Most systems are designed to trigger a filter replacement at a specific ΔP. Pressure gauges installed upstream and downstream of the filter housing provide real-time ΔP readings.
Manufacturer’s Recommended Lifespan
Manufacturers specify a general lifespan for cartridge filters, typically ranging from days to weeks, depending on their dirt-holding capacity and intended use. However, the actual lifespan may vary significantly due to factors such as contaminant concentration, flow rate, and system operating conditions.
Quality degradation in Output
Observable changes in the quality of filtered liquid, such as cloudiness, discoloration, or particulate presence, indicate that the filter is no longer effective. Similarly, in sterile applications, microbial breakthrough or contamination is a clear sign of filter failure.
Physical Condition of the Filter
Visual inspection of the cartridge can reveal excessive dirt accumulation, discoloration, or physical deformities such as cracks or warping. These are indicators that the filter must be replaced immediately.
Why Replacing a Cartridge Filter Matters
Replacing a cartridge filter isn’t just routine maintenance, it’s a critical step to keep systems running smoothly and efficiently. Filters that are clogged cause pressure to rise, forcing pumps to work harder and increasing energy costs. Over time, this strain can damage downstream equipment and disrupt entire operations.
In industries like pharmaceuticals, food and beverage, and bottled water, the consequences of poor filtration go beyond inefficiency, they can lead to contaminated products, regulatory violations, and costly production shutdown. Timely replacement ensures that flow rates remain stable, filtration quality stays consistent, and the overall system performs at its best.
How to Replace a Cartridge Filter
System Shutdown and Preparation
- Turn off the filtration system to ensure safety.
- Depressurize the system by opening the air vent valve and draining residual liquid from the housing.
- Ensure all necessary tools, including wrenches, cleaning supplies, and replacement cartridges, are ready for use.
Disassembly of Filter Housing
- Unscrew the housing lid using the appropriate tools. Exercise caution to prevent spillage or contamination.
- Detach the alignment plate, springs, and wingnuts that secure the cartridge filters.
Removal of Used Filters
- Carefully remove the spent cartridges, avoiding any disturbance to the collected debris.
- Inspect the removed filters for fouling patterns, which can provide insights into upstream inefficiencies or unexpected contaminant types.
Inspection and Cleaning of the Housing
- Examine the interior of the housing for signs of corrosion, dirt buildup, or microbial growth.
- Clean the housing thoroughly using a compatible cleaning agent. Rinse with deionized water if the application requires high purity.
- Allow the housing to dry completely before proceeding.
Installation of New Filters
- Remove the protective packaging from the new cartridges.
- For depth filters, ensure they are aligned to allow uniform flow through their layered media. For pleated surface filters, confirm proper orientation for optimal contact with the flow.
- Secure the cartridges in place using the alignment plate, springs, and wingnuts. Verify that all components are properly tightened to avoid displacement during operation.
Reassembly of Housing
- Inspect the O-ring for wear or damage. Clean and lubricate the O-ring to ensure an airtight seal. Replace it if necessary.
- Reattach and tighten the housing lid securely to prevent leaks.
System Testing and Purging
- Gradually introduce liquid into the system to prevent a sudden pressure surge.
- Purge trapped air by running liquid through the system until it flows smoothly without interruptions. Close the air vent valve once air is eliminated.
- Monitor the system for leaks, pressure stability, and flow rate consistency.
Tips to Prolong Cartridge Filter Lifespan
Maximizing cartridge filter lifespan relies on proactive maintenance and proper usage practices. In high-load systems, using pre-filtration solutions with coarser filters reduces the strain on main cartridges, preventing premature clogging. Spare filters should always be stored in a clean, dry environment, kept in their original packaging to avoid damage. Additionally, regular cleaning and maintenance of filter housings, seals, and O-rings are essential to prevent leaks and ensure efficient filtration.
Common Mistakes to Avoid
Common errors can significantly shorten filter life and reduce efficiency. Reusing disposable filters compromises their performance and risks contaminant bypass. Ignoring signs of wear and tear, such as rising pressure differentials or reduced flow rates, can lead to costly damage. Lastly, using incompatible filters for specific applications can result in filter breakdown and process contamination. Matching the filter material to chemical and thermal requirements is crucial for consistent performance and reliability.
Why Choose Gopani?
At Gopani, we provide high-quality filtration solutions for industries. Our cartridge filters are made with advanced materials to capture more dirt, offer precise filtration, and last longer. We test our filters carefully to ensure top quality. Industries like pharmaceuticals, water treatment, and petrochemicals trust our filters for their needs.
Our Product Range
Conclusion
Replacing a cartridge filter is a fundamental yet technically involved process that ensures optimal filtration efficiency and system longevity. Understanding the differences between depth and surface filters allows operators to choose the right filter for their specific needs. Adhering to a structured replacement protocol minimizes downtime, enhances operational safety, and maintains product quality. For more advanced systems, implementing automated pressure monitoring or predictive maintenance tools can further optimize filter management, reducing manual intervention and operational costs.
Gopani Product Systems
Putting Innovation in Filtration Since 1993
Who we are?
- ISO 9001:2015 Certified
- Quality Conscious
- Forward Thinking and People Positive
- Engineers and Innovators at Work
Resources
- What is Filter Cartridge?
- What is a String Wound Cartridge Filter?
- What is Melt Blown Filter Cartridge?
- What is a Pleated Cartridge Filter?
- Filtration and Separation
- Why Advanced Pre-filtration for Desalination?
- Advanced Filtration Solutions For Oil And Gas Industry
- Advanced Filtration Solutions For Chemicals & Solvents
- Advanced Filtration Solutions For Pharmaceuticals
- Process and Utilities Water Treatment
Our Trending Cartridge Filters Products
- Melt Blown Cartridge Filters
- String Wound Cartridge Filters
- Pleated Cartridge Filters
- ClaryFlow Big Buddy
- High Flow Filter Cartridges and Housings