How is a melt blown cartridge filter made?
The melt blown cartridge filters are cylindrical cartridges made from the finest polymer fibers melt blown and collected over a rotating spindle. The polymer travels through a tubular path and is blown out through the opening and the polymer steam is air dragged to form fibers. These fibers are collected on the rotating spindle to form a gradient structure and then pressed and sintered. This process of blowing fibers, rotating spindle and spinning a cartridge filter is engineered, and cartridges are spun in a controlled environment for the desired quality and variant. The fibers are spun in such a fashion that they form a density gradient, higher at the core and sparse at the outer. The most common material used to manufacture a melt blown filter is polypropylene. Very fine filter medium can filter finer/very small sediments from liquids.
The melt blown cartridge filter is also known as/referred to as spun cartridge filter or spun bonded cartridge filter.
How does a spun bonded cartridge filter work?
The filtration in melt blown cartridge filters happens “out to in”. i.e the filtration liquid flows in from the outside through the filter medium (melt blown filter cartridge) into the hollow center and is thrusted out from the outlet. The melt blown filters are available in porosities ranging from 1 micron to 50 microns.
Characteristics of a Melt Blown cartridge filter
The melt blown cartridge filters are sturdy with a fixed pore structure. The process fluids travel through the medium in a straight path and may encounter up to eight impingements on the way. The cartridge filters are widely is used in applications involving water filtration, RO pre filtration, Oils, Filtration of slightly corrosive liquids, compatible solvents and gasses. The spun cartridge filter can filter in operating temperatures up to nearly 80 Deg C.
Features to look for in a good quality pp melt blown Filter
- Good dirt holding capacity
- Premium grade materials that meet FDA standards
- Ability to sustain low pressure drop operating conditions
- Withstand mildly corrosive liquids and chemicals
- Graded density pore structure for true filtration
- Fixed pore structure
- Economical and efficient (value for money)
Found in both types:
- SOE: Single open ended – one end is sealed using a polypropylene cap.
- DOE: Double open ended – Both ends open, no end caps used
PP melt blown cartridge filter variants are used across a range of applications like:
- Water and waste water filtration
- Pre-filtration for Reverse Osmosis
- Pre-filtration in desalination
- Pre filtration for industrial water treatment systems
- Plating of metals
- Photographic fluid filtration
- Chemical filtration applications
- Textile Printing Inks and specialty coatings
- Applications involving highly viscous liquids
- Applications that involve filtration of weak acids & bases, chemicals and solvents.
How to ensure enhanced service life for a melt blown cartridge filter?
A melt blown cartridge filter should be spun in a gradient. What is the benefit of this gradient density? the gradient retains bigger sediments at the surface and smaller/finer particles at the core. this ensure that the filter does not clog frequently. Besides as we already discussed the melt blown has a fixed pore structure it means the gradient that it forms retains shape and the pores do not expand or let larger particles pass through thus ensuring filtration efficiency. When pores retain their shape and do not clog easily, it means they work consistently and efficiently for a long time.
What is a multicomponent melt blown cartridge filter?
Multicomponent melt blown cartridge filter has a layered structure. Popular multicomponent melt blown cartridge filters Media like the Claryfil Visco Q are made of non-woven and moulded layers. The cartridge filter’s layered structure allows fine filtration and increases the service life of the equipment. Such filter cartridges are equipped to handle high flow rates as compared to the regular melt blown filters.
Why are some melt blown cartridge filter variants available with grooves?
Companies like Gopani Product Systems offer pp melt blown cartridge filters with grooved structure on request. Some melt blown cartridge filter variants designed for specific applications also have a grooved structure. By adding grooves to a plain surface cartridge filter, the surface area of the filter increases and so does its dirt holding capacity. The increased surface area leads to a cleaner drop in pressure and enhances the performance of the filter.
Why use a pre-washed pp melt blown cartridge filter?
Most of the good quality melt-blown cartridge filters are prewashed. Pre-washing removes all the contaminants, surfactants and foaming agent’s residual in the filter medium. When all these contaminants are washed out before using the filter equipment, a lot of problems like chemical leaching and foaming can be avoided.
Our Resources
- What is Filter Cartridge?
- What is a String Wound Cartridge Filter?
- What is a Pleated Cartridge Filter?
- Filtration and Separation
- Why Advanced Pre-filtration for Desalination?
- Advanced Filtration Solutions For Oil And Gas Industry
- Advanced Filtration Solutions For Chemicals & Solvents
- Advanced Filtration Solutions For Pharmaceuticals
- Process and Utilities Water Treatment
Choose from an exclusive range of Melt Blown Filter Cartridge variants from Gopani Product Systems
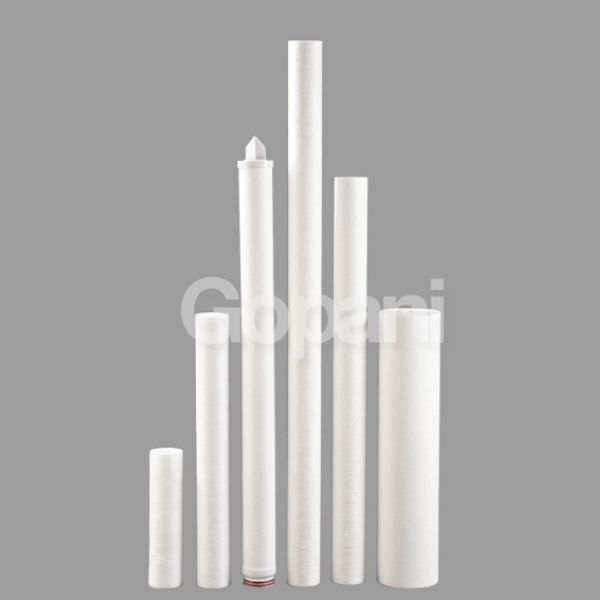
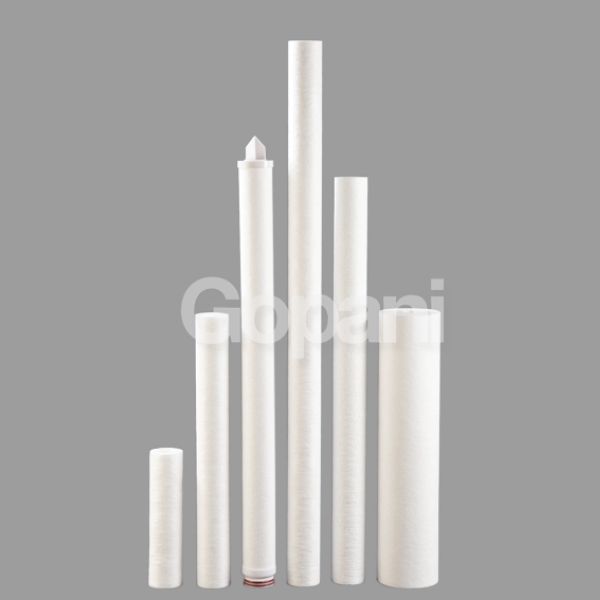
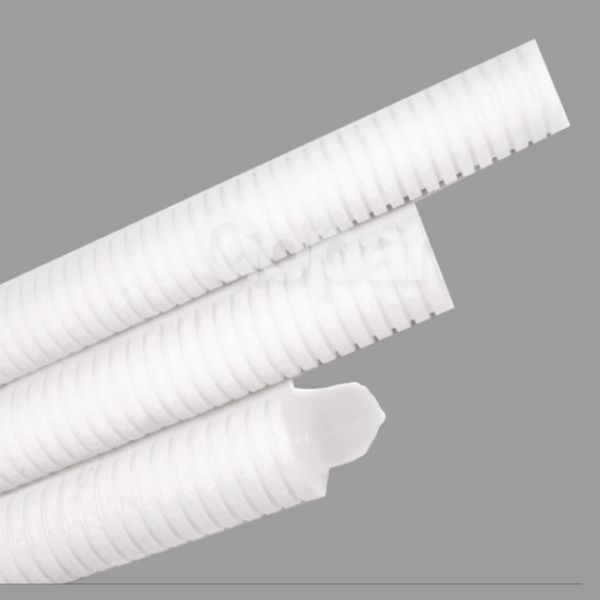
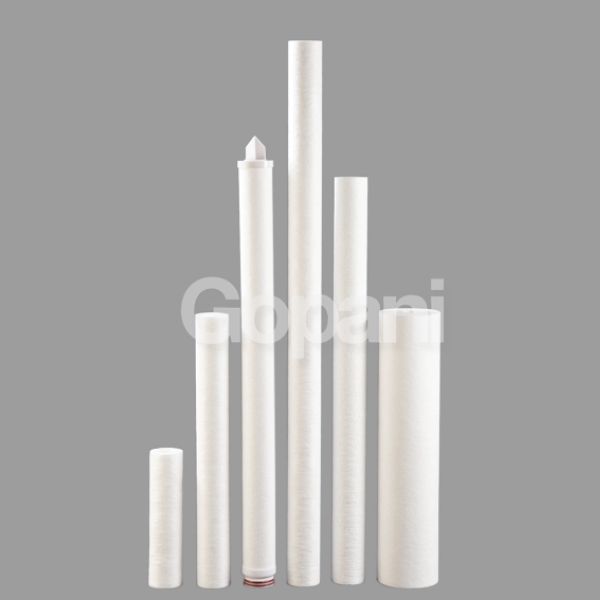
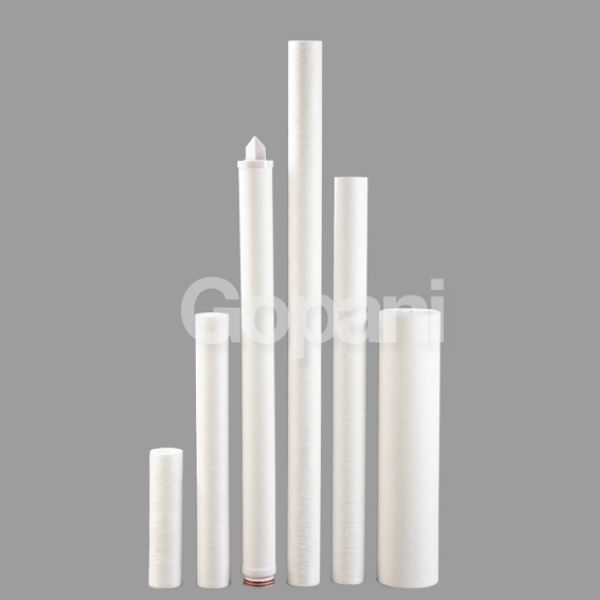
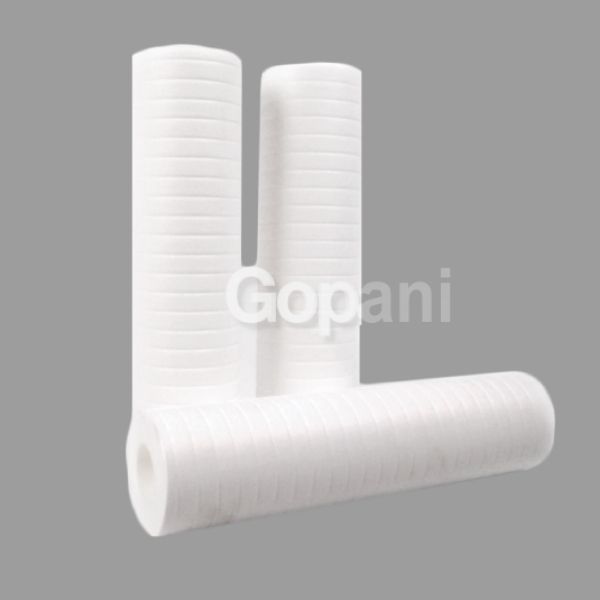
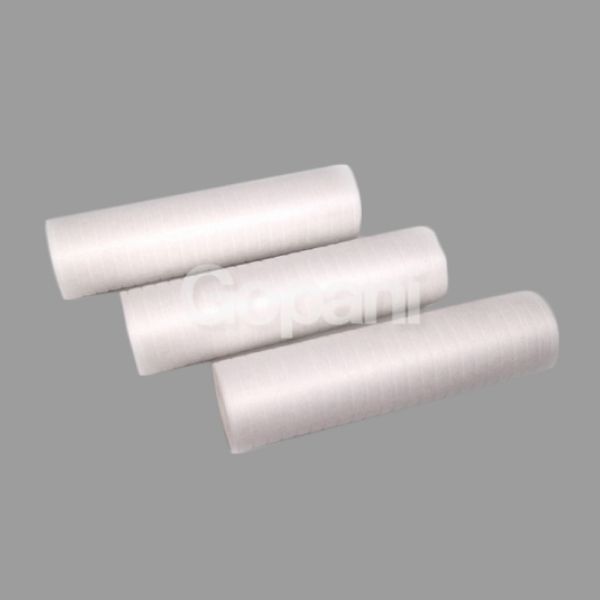
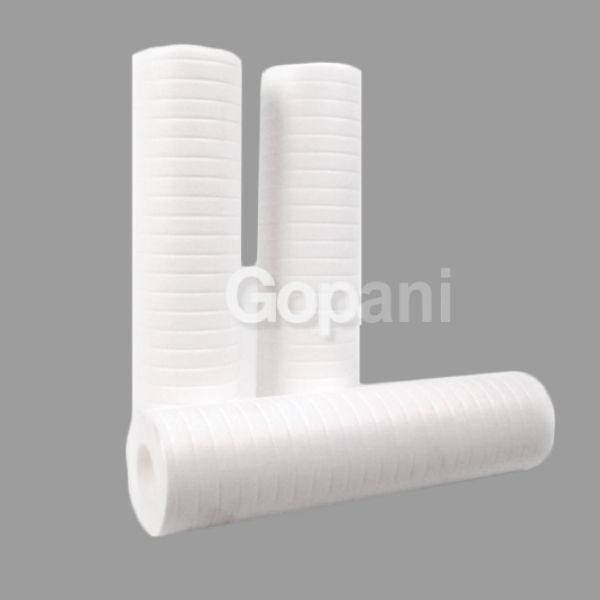
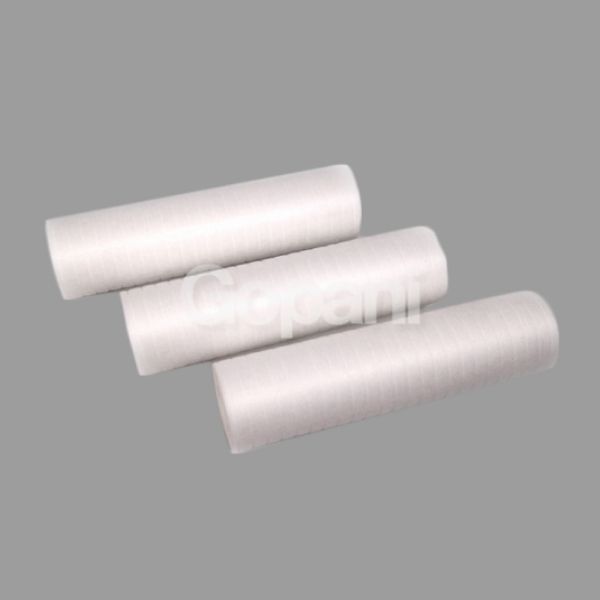
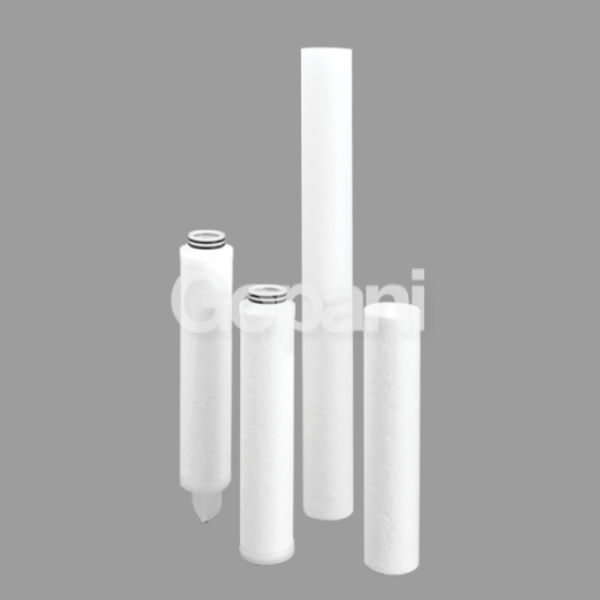
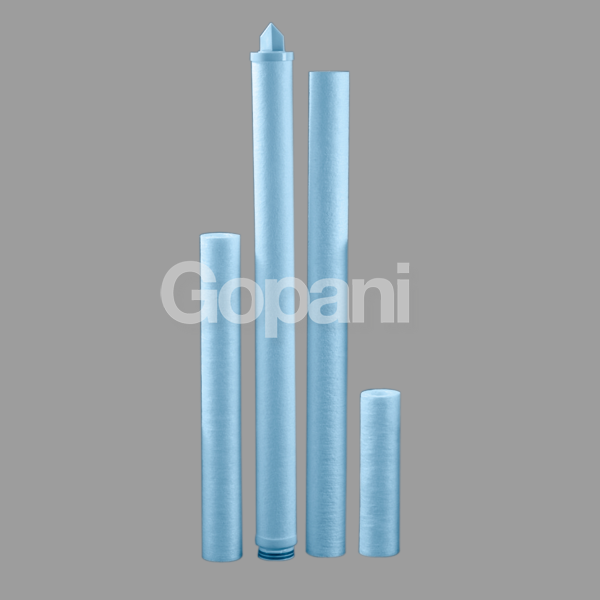