What is the difference between a string wound and melt blown filter cartridges?
There is a lot of confusion and different expert opinions when it comes to choosing or selecting a filter – and the widely asked question is “string wound or melt blown?” Conventionally if we talk about string wound and melt blown filter cartridges, melt blown variant gets a plus one as it has a fixed pore structure. Fixed pore structure means that when the filter faces differential fluids, the polypropylene fibers do not sperate – if they sperate the trapped contaminant particles might flow into the filtrate. However today, with the use of Advanced technology, high quality string wound cartridges are engineered, and this differentiation is rendered redundant.
So is the pore structure the only differentiating factor? What is the difference between a string wound and melt blown? How will you decide if string wound is the best for your application or melt blown?
(It is wise to only compare apples or oranges and not apples to oranges, so let us consider PP media for both melt-blown and string wound.)
If we deep dive, there are various factors that will influence the choice of cartridge filter. Here is a chart that will help you differentiate between a string wound and a melt blown cartridge filter and choose the best filter cartridge for your filtration requirement.
Sr No. | Character | String wound Type | Melt Blown Type |
---|---|---|---|
1 | Structure of the cartridge filter | Yarn of specific diameter is wound over a support core to form a diamond / “v”shaped pattern that creates a torturous/zigzag path for liquid to travel through offering depth filtration. String Wound cartridge filter needs a support core to wind yarn over it. | Fibres of a specific size are blown from a nozzle and thermally bonded on a rotating spindle/shaft to create a dense and porous structure that provides uniform porosity through which liquids have to pass and thus offers depth filtration. Density in such a structure can be increased/decreased depending upon the degree of filtration desired. This structure, in general, has no supporting core. |
2 | The path of Process fluid | Long torturous path due to a zig-zag diamond shape winding | Almost a straight path |
3 | The number of impingements (filtration points) in the path | More than 16 paths (calculated) | Close to 8 paths (calculated) |
4 | Single Matrices or Multi Matrices suspended solids i.e SS in narrow microns range or wide micron range | String wound cartridge filters can be produced in multi gradient structure. This allows suspended particles to penetrate deep in to the structure resulting in true depth filtration. | Melt blown cartridges can also be produced in dual/multi gradient structure. In general, it has tendency to trap the particles in outer most area resulting in unutilized inner layers. Comparatively it offers less dirt holding capacity than string wound cartridges. |
5 | Inner core | PP or SS | NA or with PP core |
6 | Concentration of SS to be removed | For higher concentration due high Dirt holding capacity. So, it can be used as a pre-filtration product prior to costly pleated filters. | Lower Dirt Holding hence for Lower SS Concentration. |
7 | Nominal or Absolute Filter | Nominal rated at efficiency around 95%. | Nominal rated at efficiency around 97%. |
8 | Type | SOE and DOE | SOE and DOE |
9 | Micron rating | From 0.5 micron to 150 micron. | 1 to 20 micron |
10 | Other filter media available | Polypropylene, Cotton, Glass Fibre | Polypropylene, Nylon |
11 | Make | Our own manufacturing with Quality Control and ISO 9001 -2015 certification | Local sourcing as well as imported ones like Savana MB of Entegris, Diwabo, Japan, Atlas Filtri. |
12 | Applications | Applications which require temperature as high as 350 deg C. Applications that has high dust load and needs depth filtration. | Temp Rating up to 120 Deg C. Applications that requires final/end point filtration. Applications in which liquid is already passed through pre-filtration stage. However, this can be used in applications that don’t have pre-filtration but little less life cycle. |
Our Resources
- What is Filter Cartridge?
- What is a String Wound Cartridge Filter?
- What is Melt Blown Filter Cartridge?
- What is a Pleated Cartridge Filter?
- Filtration and Separation
- Why Advanced Pre-filtration for Desalination?
- Advanced Filtration Solutions For Oil And Gas Industry
- Advanced Filtration Solutions For Chemicals & Solvents
- Advanced Filtration Solutions For Pharmaceuticals
- Process and Utilities Water Treatment
Explore our String Wound and Melt Blown Filter Cartridges
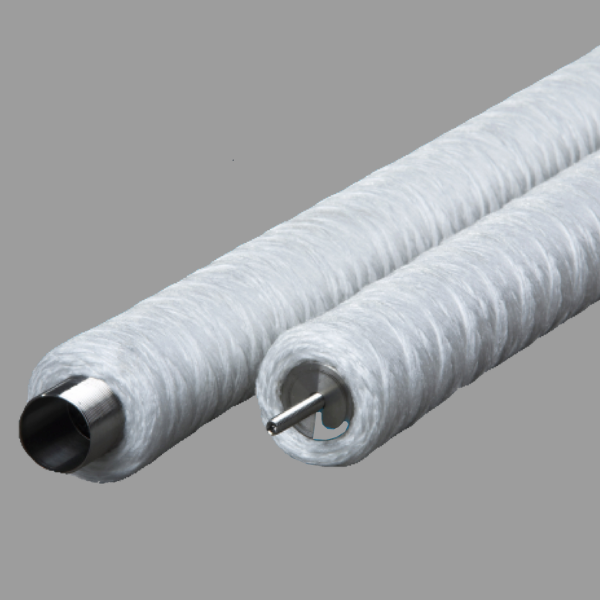
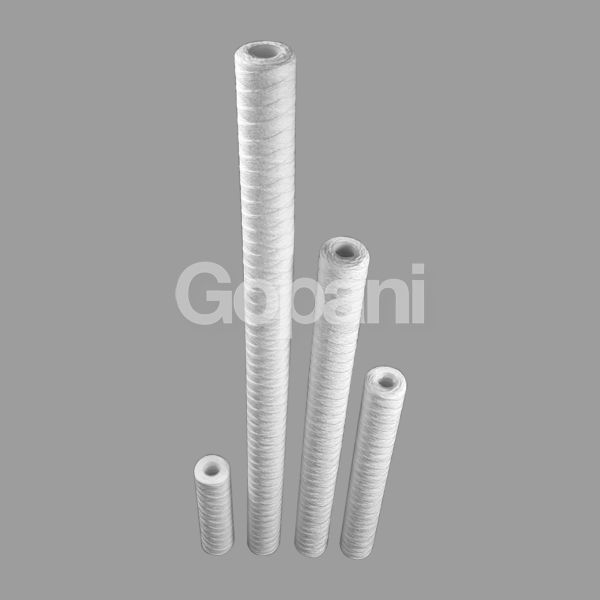
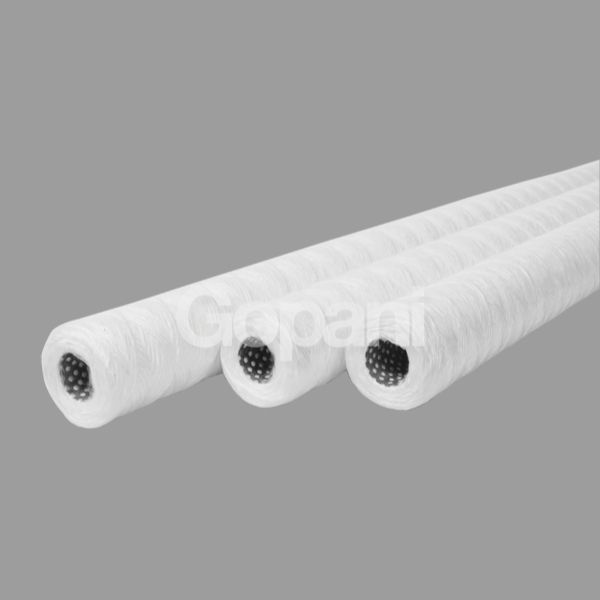
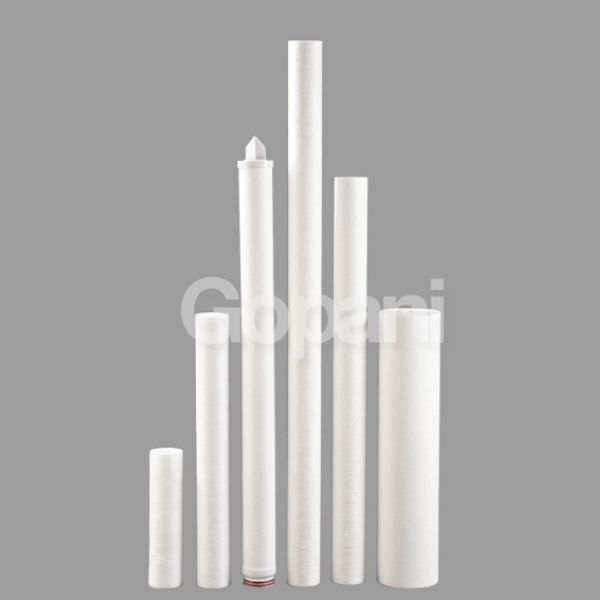
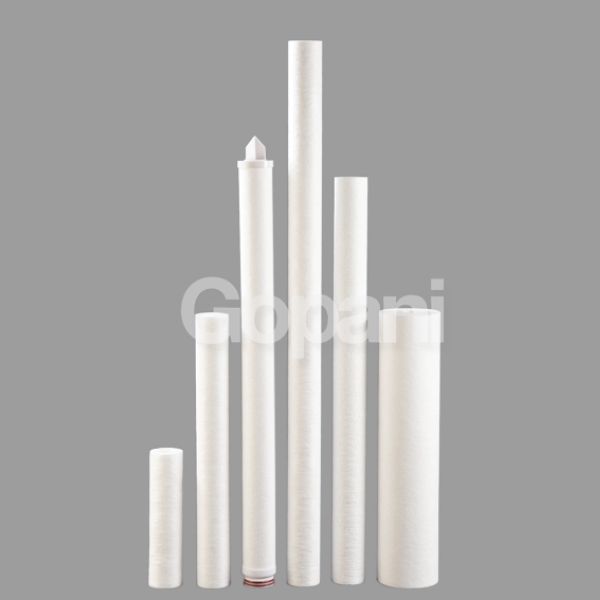
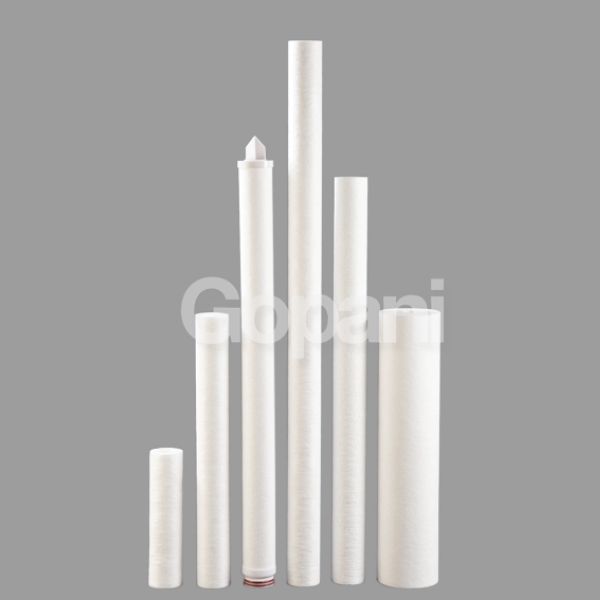
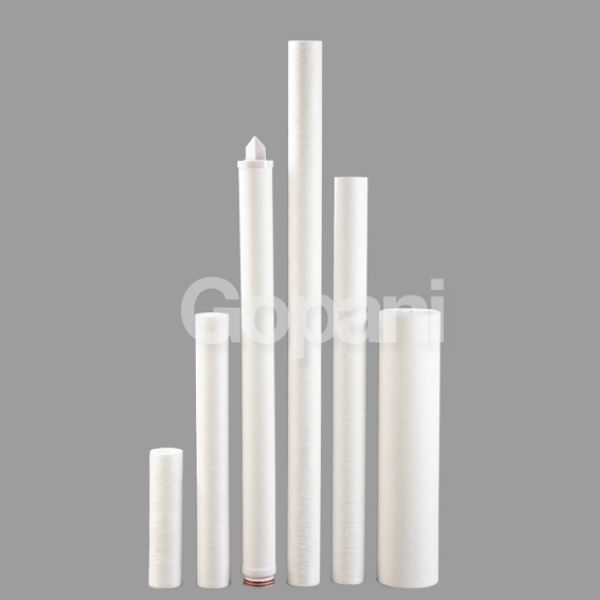
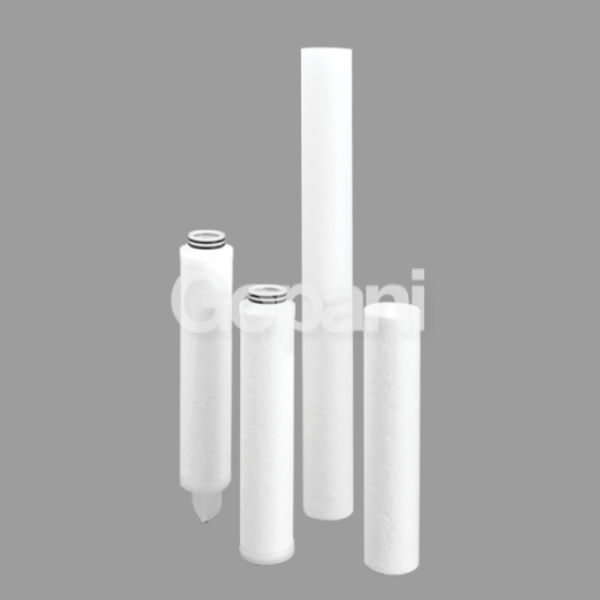
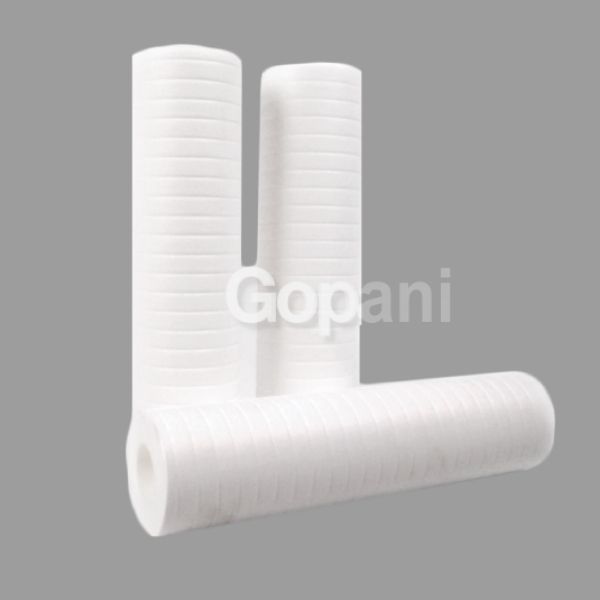
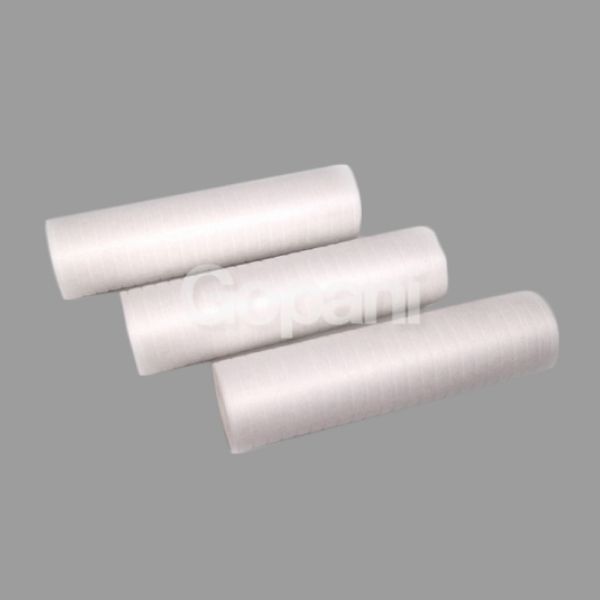
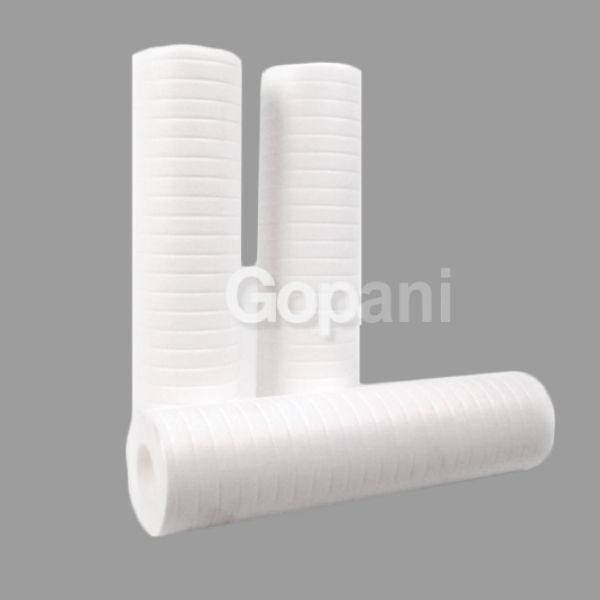
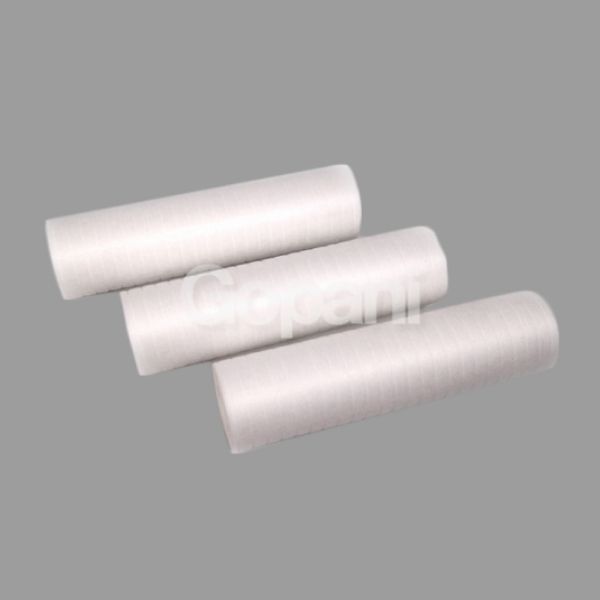
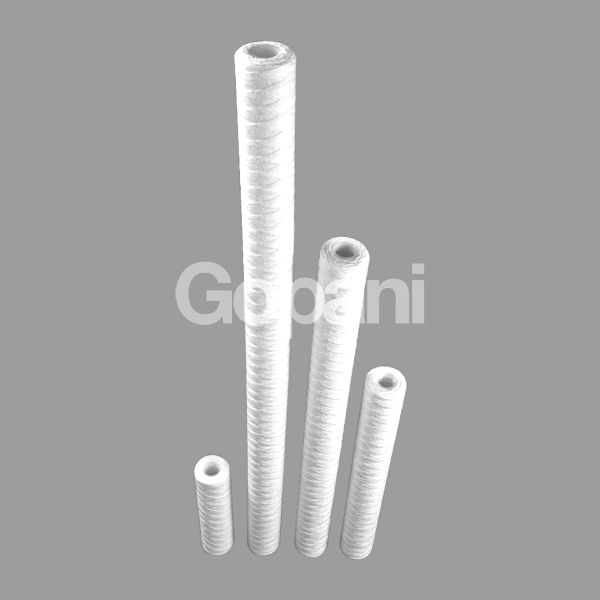
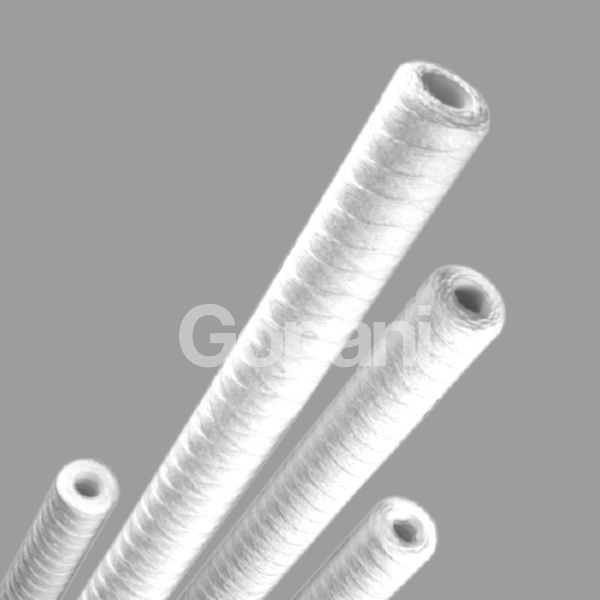