Filtration in Oil and Gas: The Role of String Wound Filters
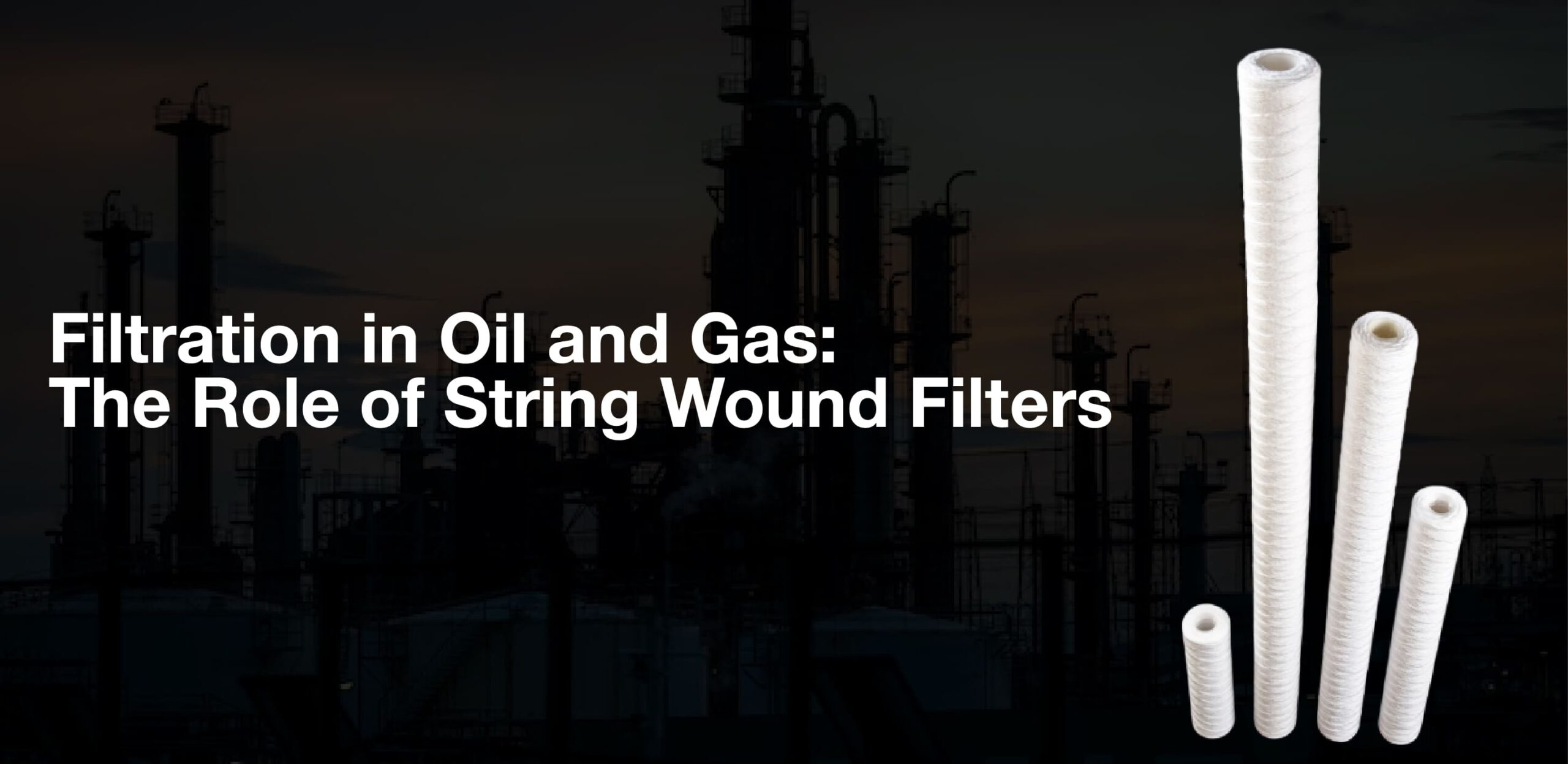
The oil and gas industry operates in tough environments that demand strong and reliable filtration systems. From extracting crude oil to refining and processing, contaminants like sand, debris, and hydrocarbons can disrupt operations. Filtration in oil and gas operations is essential to ensure smooth workflows, extend equipment life, and meet regulatory standards.
String wound filters are a dependable solution for oil and gas filtration. They are durable, hold a large amount of dirt, and effectively handle various contaminants. Their robust design makes them ideal for challenging environments, ensuring consistent performance across all stages of oil and gas operations.
This article explains the importance of filtration in the oil and gas industry, how string wound filters meet these demands, and the benefits they offer to improve efficiency, reduce costs, and support safe operations.
What Are String Wound Filters?
String wound filters are cylindrical filters constructed by winding yarn around a central core. This design creates a depth filter capable of capturing particles of varying sizes, ensuring thorough filtration.
Key Features:
- Gradient Structure: Traps both large and fine particles at different depths.
- Material Variety: Options like polypropylene, cotton, or glass fiber cater to specific fluid characteristics and temperatures.
- Durability: Handles high flow rates and harsh conditions in oil and gas applications.
Applications of String Wound Filters in Oil and Gas Operations
Filtration is critical across multiple stages in oil and gas processes. String wound filters address several challenges effectively:
Filtration of Drilling Fluids:
- Removes drill cuttings, debris, and other impurities to maintain fluid integrity.
- Ensures proper lubrication and cooling during drilling operations.
Treatment of Produced Water:
- Captures sand, silt, and hydrocarbon residues from water extracted alongside oil and gas.
- Prepares water for reinjection or safe disposal, adhering to environmental standards.
Filtration in Refinery Processes
- Protects heat exchangers, pumps, and other equipment from fouling and wear.
- Ensures consistent quality of end products like diesel, gasoline, and lubricants.
Advantages of Using String Wound Filters in Oil and Gas
String wound filters provide significant benefits that make them suitable for oil and gas operations:
- Reduces Waste: By filtering out impurities, materials can be reused, supporting sustainable practices.
- Equipment Protection: Prevents wear and fouling in critical machinery by removing contaminants.
- Operational Stability: Reduces the likelihood of unplanned shutdowns, ensuring consistent production.
- Cost Management: Longer service life and fewer replacements contribute to reduced maintenance costs.
- Environmental Compliance: Assists in meeting water and waste treatment standards by capturing harmful particulates.
Challenges in Oil and Gas Filtration
Filtration in the oil and gas industry comes with many challenges. Extreme pressure, and corrosive fluids can damage filtration systems. Contaminants like sand, debris, and hydrocarbons can block filters and harm equipment. This makes it important to use filtration systems that are strong, efficient, and reliable.
How String Wound Filters Overcome These Challenges
String wound filters are built to handle tough oil and gas conditions. They are strong enough to work under high pressure. With their ability to capture a wide range of contaminants, they keep operations running smoothly.
These filters are resistant to chemicals, last longer, and need less maintenance. Their flexibility to work in various applications, from drilling to refining, makes them a dependable solution for oil and gas filtration challenges.
How to Select the Right String Wound Filter for Oil & Gas Filtration
Picking the right string wound filter is important for smooth oil and gas filtration. Start by checking the type of fluid, temperature, and flow rate in your system. For example, filters that handle high heat or have specific micron ratings are great for thick or corrosive fluids.
At Gopani, we have a variety of string wound filters to suit your needs:
- Clarywound Cotton SS
- Clarywound Extreme Bico
- Clarywound Ultra
- Clarywound 3X
- Clarywound Extreme
- Clarywound GF
- Clarywound CPU
Need help choosing the right one? Our team is here to assist you. We can also customize filters to match your exact requirements. Contact us today for expert advice and solutions!
Gopani's String Wound Filter Solutions For Oil and Gas Filtration
Filtration in oil and gas operations is crucial for maintaining smooth workflows and protecting equipment. String wound filters are an ideal solution for oil and gas filtration, effectively handling tough conditions and capturing contaminants. Their durability, efficiency, and cost-effectiveness help ensure operational stability and regulatory compliance. Selecting the right string wound filter based on fluid properties and system requirements is essential for optimal performance.
At Gopani, we offer a wide range of string wound filters designed to meet the specific demands of the oil and gas industry. Visit Gopani to explore our solutions or contact our team for expert guidance in finding the right filters for your needs.
FAQs
Q 1: Why are string wound filters ideal for the oil and gas industry?
Their robust design, high dirt-holding capacity, and ability to handle various contaminants make them suitable for the tough conditions in oil and gas operations.
Q 2: What materials are used in string wound filters?
They can be made from polypropylene, cotton, glass fiber, and other materials, with cores often made from polypropylene or stainless steel.
Q 3: How do string wound filters protect equipment in the oil and gas industry?
By removing contaminants like sand, debris, and hydrocarbons, these filters prevent wear and fouling in critical machinery, extending equipment life.
Q 4: What are the key applications of string wound filters in oil and gas operations?
They are used in the filtration of drilling fluids, treatment of produced water, and refinery processes to protect equipment and ensure product quality.
Q 5: How do I select the right string wound filter for my application?
Consider the fluid properties, flow rate, pressure, and contaminant size. Choose filters with appropriate materials and micron ratings for your specific needs.
Q 6: Can string wound filters handle high temperatures?
Yes, glass fiber string wound filters are suitable for high-temperature environments commonly found in oil and gas operations.
Q 7: What are the benefits of using string wound filters in oil and gas processes?
They enhance product quality, protect equipment, ensure operational stability, reduce maintenance costs, and help meet environmental compliance standards.
Gopani Product Systems
Putting Innovation in Filtration Since 1993
Who we are?
- ISO 9001:2015 Certified
- Quality Conscious
- Forward Thinking and People Positive
- Engineers and Innovators at Work
Resources
- What is Filter Cartridge?
- What is a String Wound Cartridge Filter?
- What is Melt Blown Filter Cartridge?
- What is a Pleated Cartridge Filter?
- Filtration and Separation
- Why Advanced Pre-filtration for Desalination?
- Advanced Filtration Solutions For Oil And Gas Industry
- Advanced Filtration Solutions For Chemicals & Solvents
- Advanced Filtration Solutions For Pharmaceuticals
- Process and Utilities Water Treatment
Our Trending Cartridge Filters Products
- Melt Blown Cartridge Filters
- String Wound Cartridge Filters
- Pleated Cartridge Filters
- ClaryFlow Big Buddy
- High Flow Filter Cartridges and Housings