String Wound Cartridge Filters for Chemical Filtration, Processing, and Production
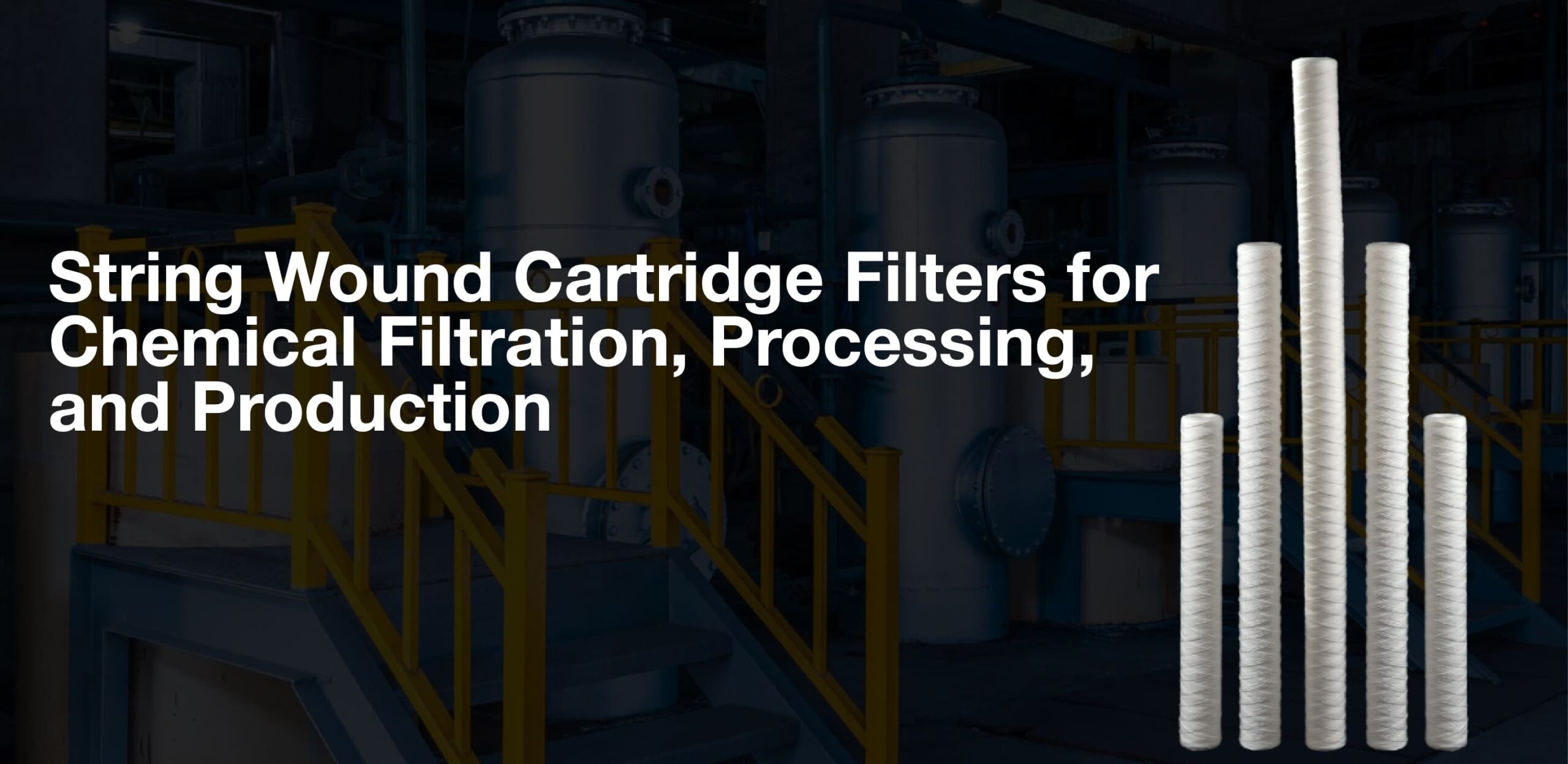
Chemical filtration plays a very important role in ensuring the reliability of the process, protecting the equipment, and guaranteeing the quality of the final product in chemical production
Efficient and reliable approaches to handling aggressive chemicals and ensuring fluid purity lead us to the some choice of the String Wound Cartridge Filter for Chemical Filtration.
These filters are cylindrical-shaped filtration elements constructed of yarn (string) wound around a core. This setup creates a density gradient, allowing particles of multiple sizes to be trapped all throughout the filter.
In today’s production processes, string wound cartridge filters are one of the best chemical filtration options available. This blog contains benefits, applications, and selection tips for string wound cartridge filters are included in this article.
Key Aspects Include:
- Materials: Polypropylene, fiberglass, cotton, and nylon, with cores made of polypropylene or stainless steel for better durability.
- Micron Ratings: 0.5 to 150 microns.
Performance Features:
- High dirt-holding capacity allows fewer changes.
- Gradient in the density to trap the particle correctly.
- Gradient density for, efficient particle trapping.
Importance of Filtration in Chemical Production
- Ensures Product Quality: Filtration removes unwanted particles, making sure the final product meets quality standards.
Protects Equipment: By keeping pumps and valves running smoothly, removing contaminants prevents damage to moving parts and ultimately saves expensive repairs.
Enhances Operational Efficiency : Clean fluids ensure the smooth functioning of the process, thereby minimizing downtime and enabling higher productivity.
Complies With Safety Measures: By eliminating hazardous impurities in chemicals, filtration eventually complies with the safety regulations.
Decreased Waste: With the filtering of impurities, materials can be reused and sustainability practices can be supported.
String Wound Filters in Chemical Production
Pre-filtration for Liquid Chemicals: String wound filters are widely used for pre-filtration in chemical production, particularly when dealing with liquid chemicals. They effectively remove large particles and contaminants before the liquids enter more sensitive parts of the production process, ensuring cleaner inputs for the next stages.
- Filtration of Aggressive Chemicals: String wound filters made with glass fiber and stainless steel cores are ideal for corrosive environments. These filters are used in: Acid and alkali processing. Solvent recovery systems, where maintaining chemical purity is critical.
- Removal of Particulates from Process Fluids: By capturing impurities like rust, scale, and organic particulates, string wound filters: Protect downstream equipment such as pumps and membranes. Ensure clear and contaminant-free outputs, enhancing the reliability of chemical formulations.
- Removal of Particulates in Adhesives, Paints, and Coatings Production: In the production of adhesives, paints, and coatings, string wound filters play a crucial role in removing particulates like dust and organic matter. By capturing these impurities, they help achieve smooth and defect-free final products while protecting equipment such as mixers and pumps.
- Filtration in Solvent Recovery Systems: String wound filters are used in solvent recovery systems to ensure the chemical purity of recovered solvents. This filtration helps remove contaminants that could degrade the quality of the solvent, ensuring it can be reused in the production process.
- Protection of Sensitive Equipment: By effectively capturing particles like rust, scale, and organic matter, string wound filters protect sensitive downstream equipment such as pumps, valves, and membranes, reducing the risk of wear and tear, and prolonging equipment life.
Benefits of Using String Wound Filters in Chemical Processes
The advantages of string wound filters extend beyond basic filtration. Here’s how they contribute to chemical processes:
- Enhanced Product Quality: By capturing contaminants efficiently, the filters ensure consistent purity in end products.
- Longer Equipment Lifespan: Preventing the accumulation of debris reduces wear and tear on machinery.
- Cost-Effectiveness: Durable construction minimizes filter replacement frequency, saving maintenance costs.
- Safe Operations: Reliable filtration prevents unexpected process disruptions and reduces risks from contaminated fluids.
Case Example: String Wound Filters in Action
A chemical plant producing industrial-grade solvents faced frequent equipment downtime due to particulate contamination. After implementing polypropylene string wound filters, the plant observed:
- Reduced filter replacement frequency by 40%.
- Improved process stability, minimizing interruptions.
- A significant decrease in maintenance expenses.
This practical shift showcased the capability of string wound filters to manage high-contaminant loads effectively.
How to Select the Right String Wound Filter for Chemical Production
When choosing a string wound filter, consider the chemical composition of fluids, temperature requirements, and flow rates. Filters with high-temperature resistance or specific micron ratings can address particular challenges, such as handling viscous or corrosive fluids.
We offer a wide range of string wound filter variants, including:
- Glassfiber
- Cotton
- Nylon
- Polypropylene
- Polyester
Made for:
- High Temperature
- High Ph Level
- Low Ph level
- Chemical Compatibility
Core Material:
- Stainless steel 316/316L and 304
- Polypropylene
- Upvc
- Cpvc
- PVDF
If you have any questions or need assistance, don’t hesitate to reach out—our experts at Gopani are always ready to help. We can also customize filters according to your specific requirements.
Gopani’s String Wound Filters
String wound filters provide reliable solutions to many challenges in the chemical industry for chemical filtration. Gopani offers a range of string wound filters, including the Clarywound Extreme, designed for demanding environments. Learn more about our filtration solutions to support your chemical processes by visiting www.gopani.com or contact our team for detailed assistance.
Gopani’s Other Filtration solutions
Check out our Other filtration solutions: pleated filters, melt-blown filters, filter bags, and filter housings. Built for diverse industrial challenges, they offer unmatched performance and durability. Whether you need efficient particle removal or sturdy containment, we’ve got you covered. Enhance your operations with our innovative and reliable products.
Gopani sintered metal filters
For those extreme industrial conditions, sintered stainless steel filters are unbeatable. Built tough and precise, they handle high temps, corrosive chemicals, and mechanical stress with ease. Their unique design guarantees consistent performance, making them a must-have for industries that need reliability and durability. Boost your operations with the power of sintered stainless steel filters.
FAQs
Q 1: What types of chemicals are string wound filters suitable for?
String wound filters are compatible with a wide range of chemicals, including acids, bases, and solvents, depending on the material of construction.
Q 2: Can string wound filters handle high-temperature conditions?
For such applications, we recommend using our sintered powder metal filter range.
Q 3: How do I choose the right micron rating for my chemical filtration?
Consider the particle size to be filtered and the desired level of clarity. Our experts can guide you based on your specific application.
Q 4: How do I place an order for string wound filters for my chemical filtration needs?
Simply contact us via our website, email, or phone. Provide your application details to help us recommend the best product.
Gopani Product Systems
Putting Innovation in Filtration Since 1993
Who we are?
- ISO 9001:2015 Certified
- Quality Conscious
- Forward Thinking and People Positive
- Engineers and Innovators at Work
Resources
- What is Filter Cartridge?
- What is a String Wound Cartridge Filter?
- What is Melt Blown Filter Cartridge?
- What is a Pleated Cartridge Filter?
- Filtration and Separation
- Why Advanced Pre-filtration for Desalination?
- Advanced Filtration Solutions For Oil And Gas Industry
- Advanced Filtration Solutions For Chemicals & Solvents
- Advanced Filtration Solutions For Pharmaceuticals
- Process and Utilities Water Treatment
Our Trending Cartridge Filters Products
- Melt Blown Cartridge Filters
- String Wound Cartridge Filters
- Pleated Cartridge Filters
- ClaryFlow Big Buddy
- High Flow Filter Cartridges and Housings