A Complete Guide - How To Maximize Recovery of Precious Metals from Spent Catalyst
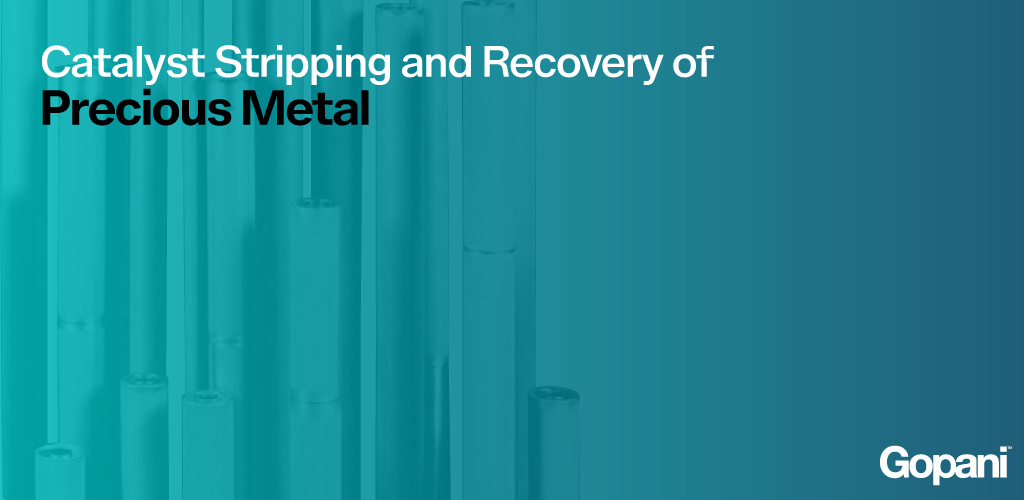
Many chemical, petrochemical and pharmaceutical processes use catalysts bearing precious metals like platinum, palladium, rhodium and gold. After repeated usage when the catalyst becomes totally deactivated, precious metals are recovered from the catalyst and its value is maximized.
At every step of recovery, filtration is one of the prime requirements. The extraction is done in multiple stages ensuring recovery to +99.95%. Gopani Products Systems has wide range of filtrations solutions specific for applications across the whole process and every step of Catalyst Recovery.
A simplified diagram of Catalyst recovery:
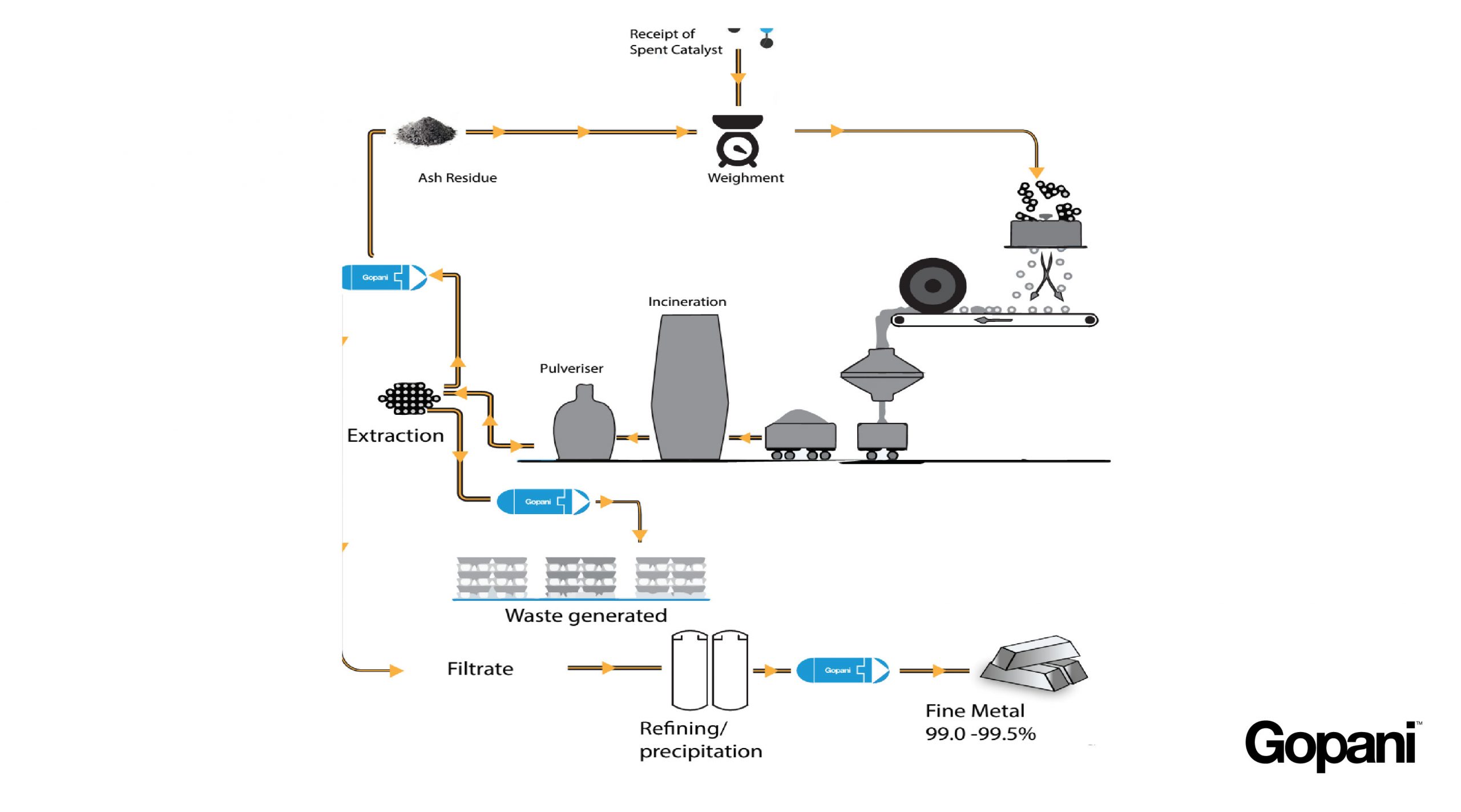
Recovery of last traces of precious metal
In any bulk Catalyst metal recovery, the metal content is firmly assessed by representative sampling methods. It is thoroughly analysed, and sometimes third parties are also involved. The third-party analysis is sometimes a mandatory requirement in a sale deed between spent catalyst seller and recovery processer. The commercial aspects are settled on the basis Metal Content, as the Catalyst Processor needs an assurance of minimum metal content extraction for commercial viability.
There are two distinct types of catalyst:
- Catalyst with Combustible support. (like Carbon)
- Catalyst with non – combustible Support. (Like Alumina, Doucil etc.)
Precious metals are recovered from the spent catalyst via a series of processes names:
- Drying. (applicable for both types)
- Analytically estimated precious metal content. (applicable for both types)
- Incineration. (applicable for both types)
- Pulverization
- Extraction or dissolution of precious metal (applicable for type A)
- Filtration for suspended solid. First step of purification. (applicable for both types)
- Control pH to precipitate any other extracted /or dissolved other metallic imparity. This step is specific for specific impurity (Specific)
Here’s a detailed flowchart that shows the entire cycle:
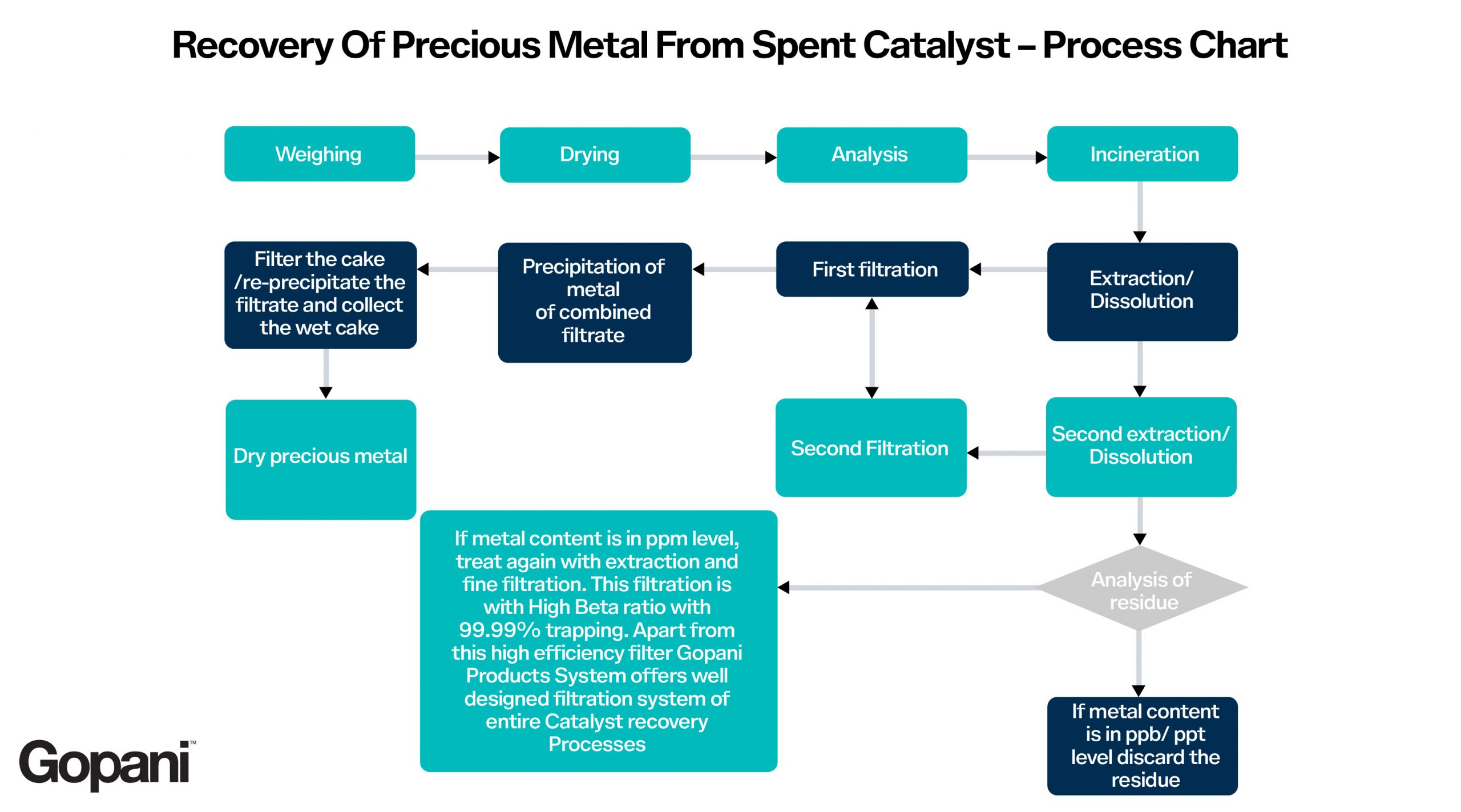
The whole process ensures that the recovery of the precious metal is to the fullest in line with the Analytical Value.
At Gopani Products Systems a complete solution can be offered based on the desired recovery and process parameters. We have an extensive range of Filter cartridges and a host of filtration systems engineered to give the best results in precious metal recovery from spent catalysts.
Expert Advice!
Our experts have extensively worked with special metal recovery units, and have vast experience and understanding of problems that may slow down or adversely affect the recovery process. Based on this experience we have prepared a chart specifying the equipment, applications, and the usual problems one may face, and most importantly – the solutions.
Cartridges and filtration systems used for various filtration applications of precious metal recovery – the problems that you may encounter and how to solve them?
No | Cartridge Type | Applications | Usual problems | Solution |
1. | Sinter Metal cartridges |
|
|
|
2. | Glass fiber wound, with SS core |
|
|
|
3. | PP wound with SS core cartridges |
|
|
|
4. | Pleated Cartridges |
|
|
|
5. | Encapsulated Cartridges |
|
|
|
tivated carbon | filter cartridges | cartridge filters | activated carbon filter | filter bags manufacturer | bag filter system | filter housin
The whole process involves the use of a series of cartridge filters and filtration systems and the sequence is specific to batch size, type of precious metal and the recovery expected. Companies choose refiners after a thorough analysis and research; hence it is of utmost importance for the refiners to maintain goodwill and to build a reputation by using the best filtration equipment available. Partner with Gopani for the best, long lasting and high performing filtration equipment for precious metal recovery from spent catalysts.
Gopani products Systems has all types filter systems with housings of different flow rates and desired efficiency.
Gopani Product Systems
Putting Innovation in Filtration Since 1993
Who we are?
- ISO 9001:2015 Certified
- Quality Conscious
- Forward Thinking and People Positive
- Engineers and Innovators at Work
Resources
- What is Filter Cartridge?
- What is a String Wound Cartridge Filter?
- What is Melt Blown Filter Cartridge?
- What is a Pleated Cartridge Filter?
- Filtration and Separation
- Why Advanced Pre-filtration for Desalination?
- Advanced Filtration Solutions For Oil And Gas Industry
- Advanced Filtration Solutions For Chemicals & Solvents
- Advanced Filtration Solutions For Pharmaceuticals
- Process and Utilities Water Treatment
Our Trending Cartridge Filters Products
- Melt Blown Cartridge Filters
- String Wound Cartridge Filters
- Pleated Cartridge Filters
- ClaryFlow Big Buddy
- High Flow Filter Cartridges and Housings